Startups are the Most Vulnerable to Supply Chain Disruptions
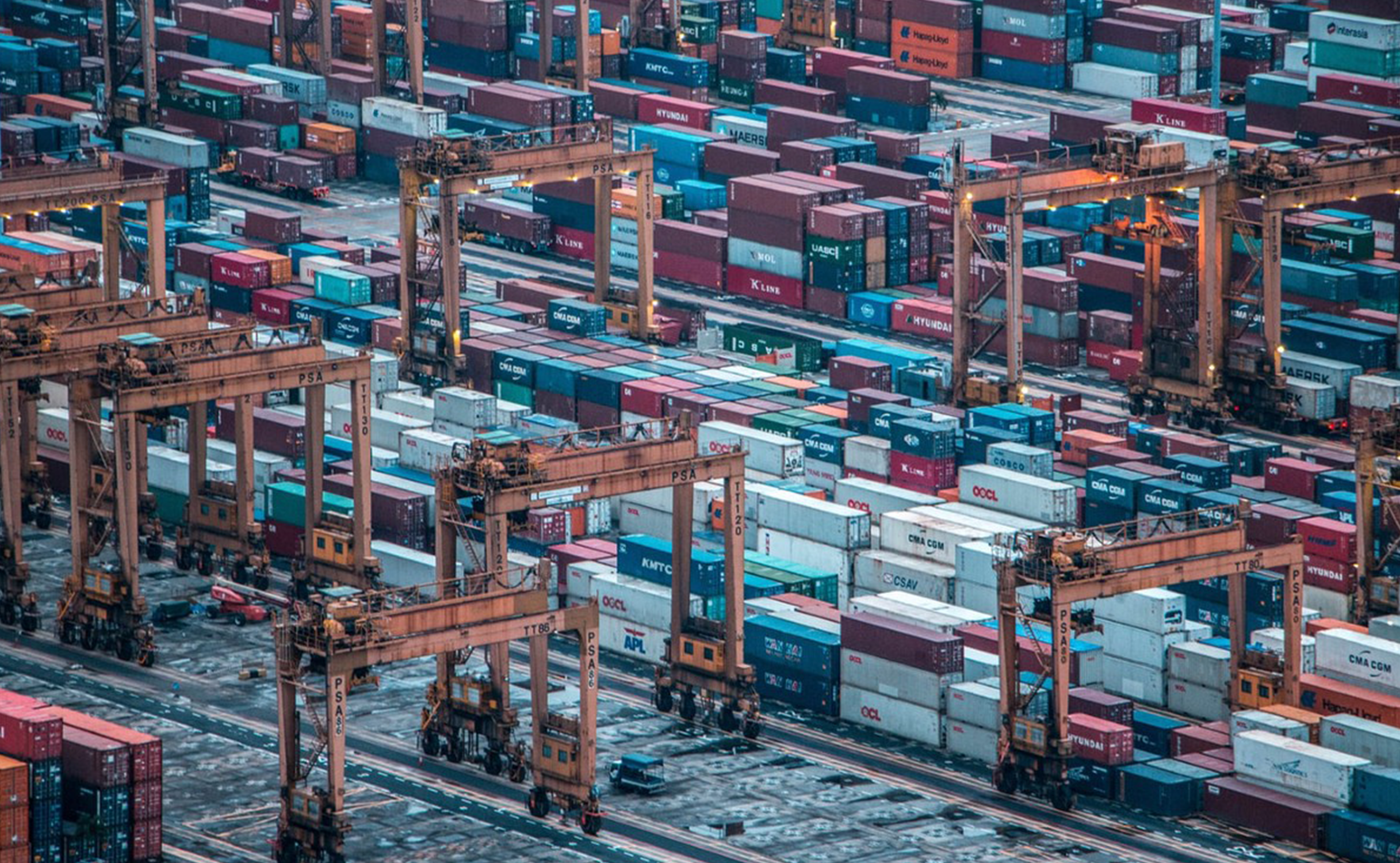
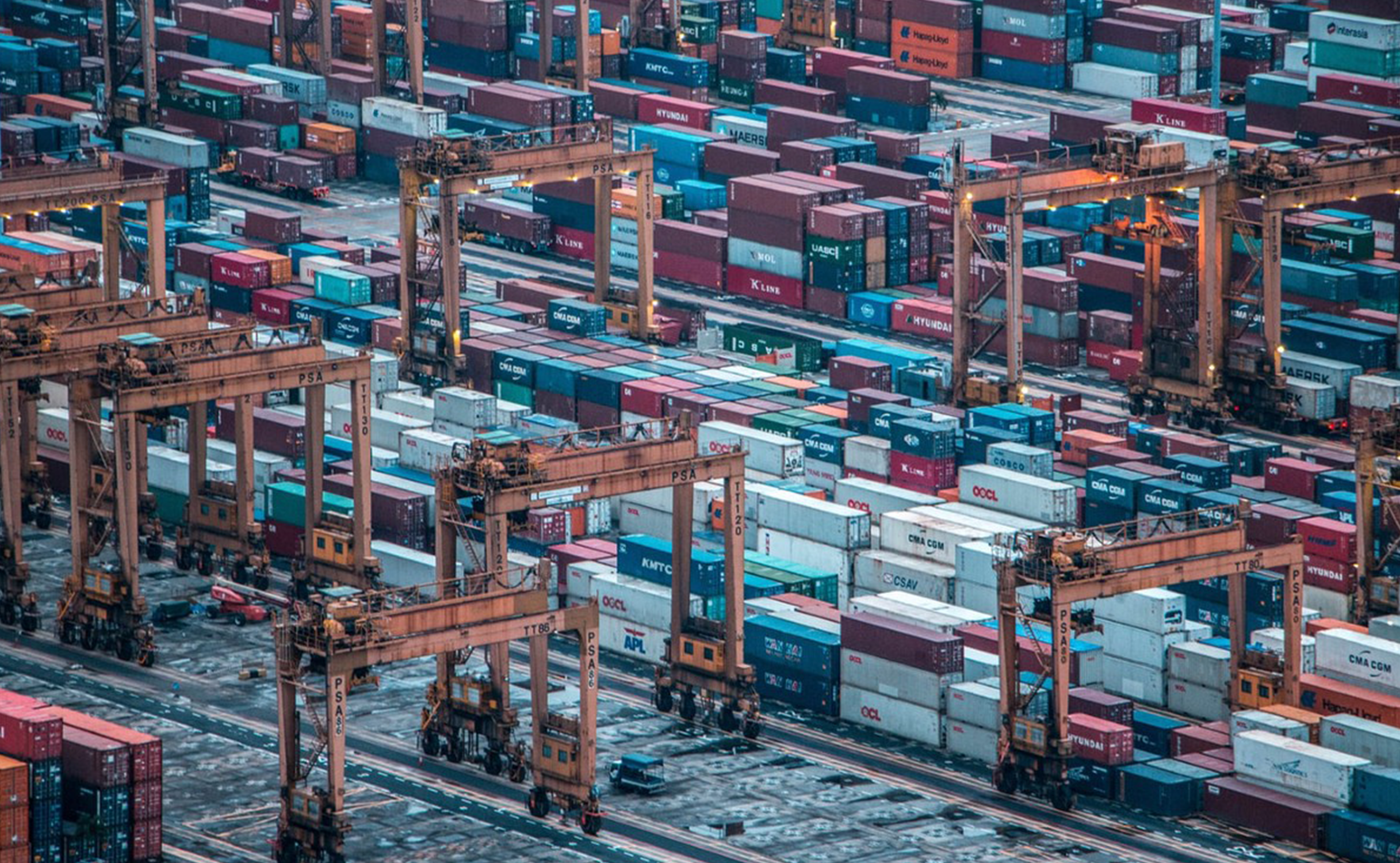
As the world grapples with the ongoing medical crisis, the global supply chain is being forced into a major restructuring — and has never appeared so fragile.
But if you’re reading this, you’re probably the kind of person that already knows this. I’m no market analyst but since I haven’t seen much about the impact on small businesses, I wanted to share the stories of the impact the pandemic has had on startups like Voltera.
How the pandemic affected small businesses
While on a recent conference call with other startups, one company discussed how they were shutting down due to the unavailability of key parts.
They manufacture sensors for building control systems that use thermal imaging sensors. Due to the massive influx in demand from the medical industry, cost-effective thermal sensors have been completely sold out.
When you are part of a small team that works at a start-up, you’re acutely focused on getting to market and testing product-market fit. What you’re not focused on (and nor should you be) is supply chain resiliency.
Unfortunately, black swan events do occur. If you haven’t taken efforts to protect yourself and are not monitoring global events, you can get caught unaware as this company did with their thermal sensors.
The timeline
I began monitoring the news of the virus in December when our Chinese suppliers began suggesting their lead times would change.
Fortunately, not only are the majority of our custom parts manufactured here in Canada, but our most recent big shipment of off-the-shelf Chinese parts was already in a shipping container making its way across the Pacific.
Because of these early warnings, those of us in North America who frequently purchase from China had a preview of things to come.
At the end of January, China had closed its factories to try and contain the epidemic. In February, delays from health-related closures were compounded by Lunar New Year closures.
In early March, after 6 weeks of closures, factories in China were allowed to reopen. However, the relief that many people were likely hoping for did not come. Immediately, the problem became worse due to two key factors: pent up demand and disrupted distribution.
Bottlenecked demand
Once reopened, suppliers were inundated with backorders. In fact, many are still catching up. While this seems like a good problem for them to have, they have struggled to produce at pre-COVID rates.
Each factory had to implement new safety restrictions that took time to implement and that slowed throughput. With each supplier that your part has to travel through before it gets to you, the lead times were compounded again and again.
No doubt this was all worsened by some factories remaining closed, by roadblocks and travel restrictions, by limited storage capacity, by loss of workforce, and by delays in communication with clients since North American companies were beginning remote work / shelter-in-place by this point.
Disrupted distribution
As parts finally began to roll off the lines, suppliers began to struggle to move them to their clients.
When I say suppliers, I mean suppliers in all geographies.
In March and April, we saw an 80–90% reduction in cargo capacity as airlines were forced to ground commercial flights in Europe, North America, and the rest of the world.
In an effort to slow the spread of the virus by canceling business and vacation traveling also meant commercial goods could no longer piggyback on international air travel which makes up 35% of world trade by value.
As you can see in the images above and below, changes to air freight capacity were felt immediately. Ocean freight was still an option (although it too was slowed down) but only if you had the time to wait for it.
How many start-ups do you know that can afford that luxury?
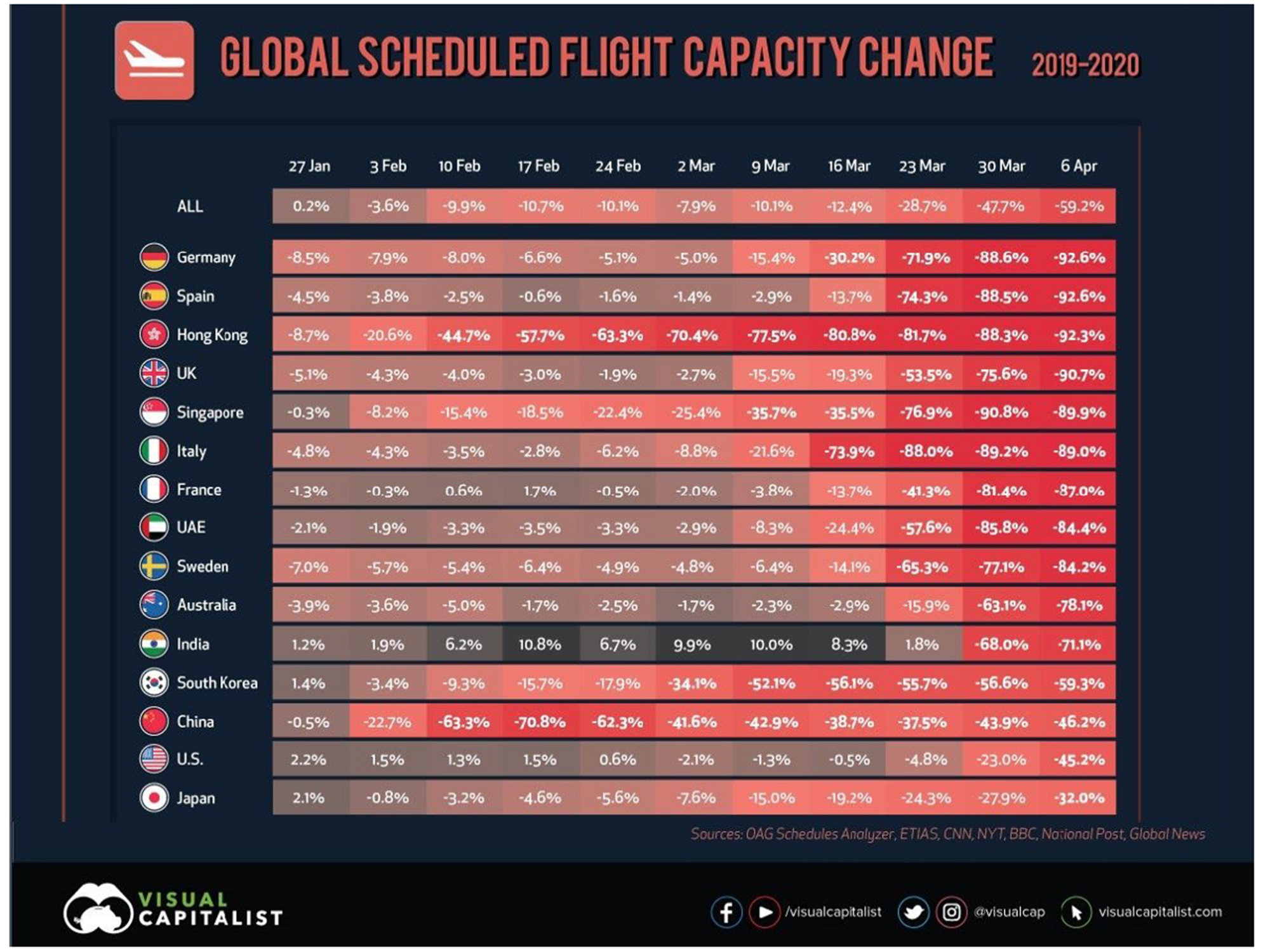
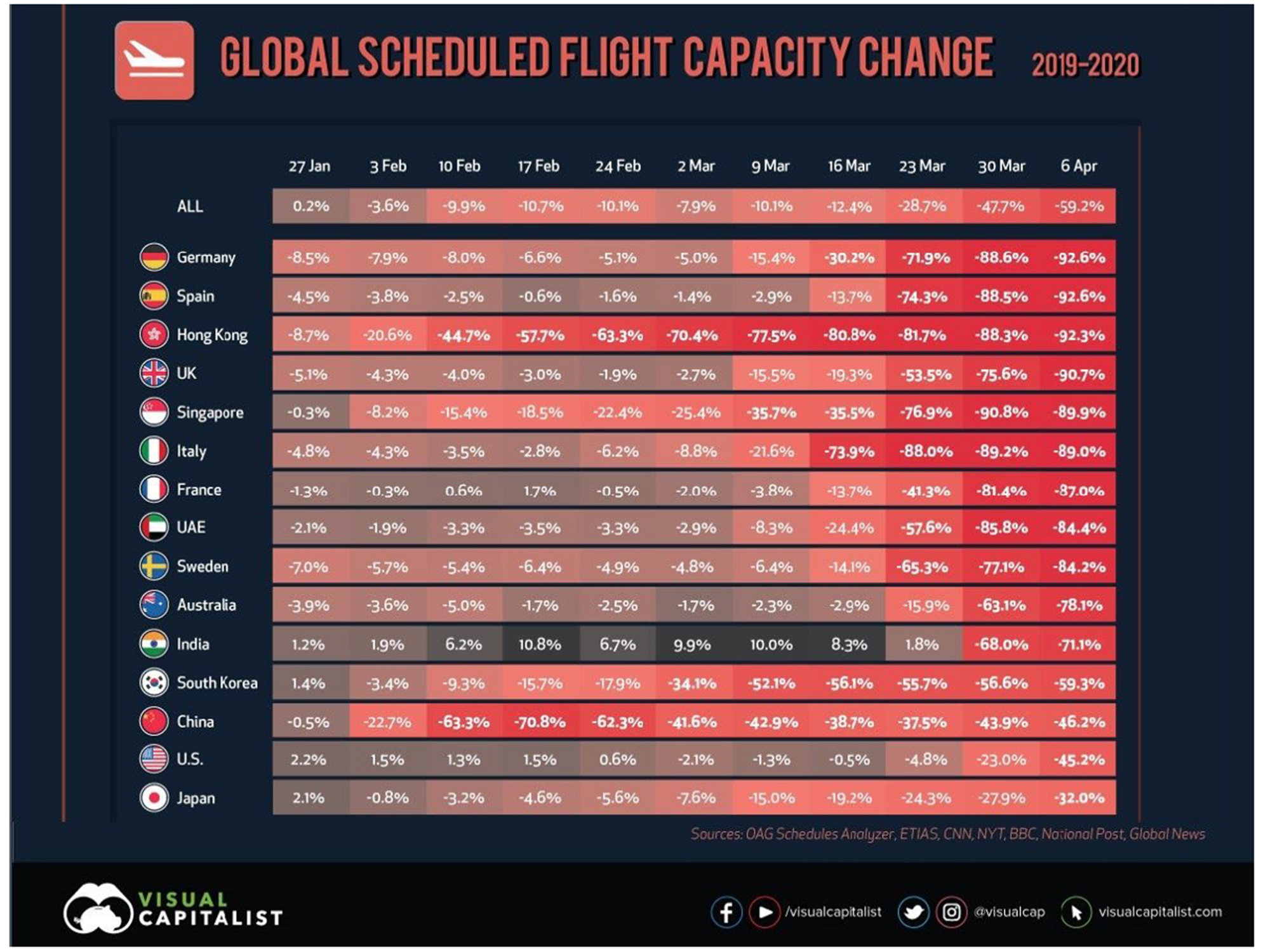
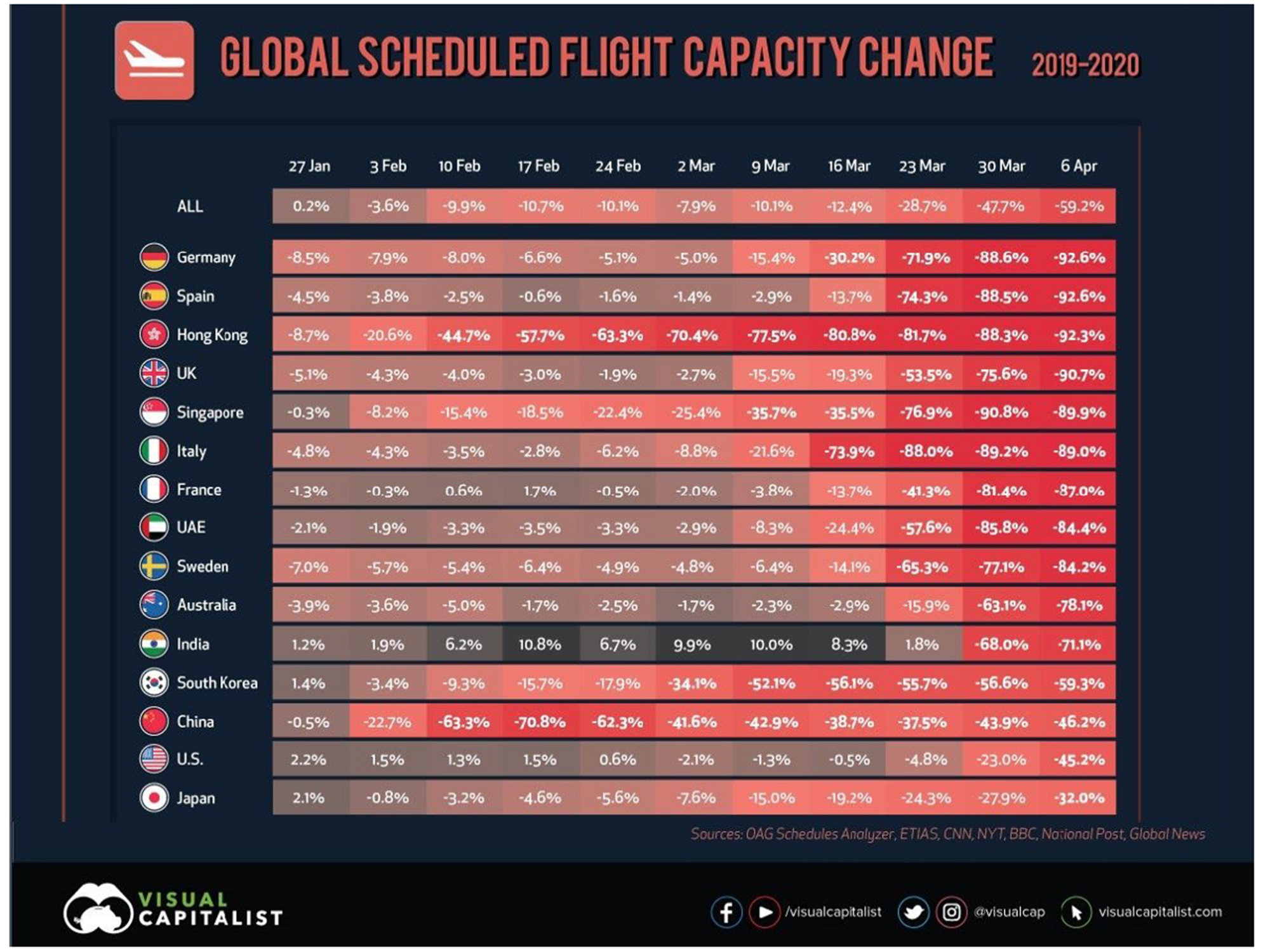
Fortunately, like many other companies, the building control startup didn’t purchase from overseas suppliers. Unfortunately for them, in a global crisis, that doesn’t matter.
While the global supply chain can withstand minor disturbances, the closing of China’s factories for 6 weeks, companies around the world beginning remote work, and the halting of international travel is not minor. The impact of these necessary decisions has spread like the virus itself.
The impact on our supply chain
Some companies had taken precautions to build up immunity. Others did not and suffered the consequences. This consequently impacted the businesses that relied on it, and so and so forth.
The fact that all companies in the manufacturing space rely on each other in some capacity shows incredible collaboration and tolerance but also means we’re prone to the domino effect.
I’m not trying to call out the companies that did not prepare. Heck, Voltera has seen minimal impact but only through sheer luck.
However, there is a reason why small businesses are usually hurt the most in times of crisis. As I alluded to, they are focused on short term survival, not long-term resilience.
That being said, even large companies have impacted by the supply chain virus. HP has reported close to a 20% decrease in their printing division sales which was “driven by supply-chain disruptions”. Apple, Google, Dell, and Microsoft have reported similar disruptions and have already looked to set up manufacturing facilities in Vietnam and Thailand.
Lessons we've learned
Companies of all sizes need to follow the example of these manufacturing giants by shifting manufacturing away from China. Rising labor costs, continuing quality concerns, the imposition of tariffs, and regulatory barriers have caused companies to re-examine the efficiencies of their supply chains. This movement started long before COVID-19, but will now be a greatly accelerated initiative.
Large companies are looking to shift their manufacturing to new places like India, Malaysia, Thailand, Vietnam, Thailand. Others are looking domestically for answers to their supply chain issues.
Although sourcing domestically has higher labor costs, you remove many of the quality control and logistics costs and headaches that come from sourcing overseas.
We have incredible relationships with all our suppliers in China because of how they do business, how they communicate, and the quality they provide us, however, we only got to this point after many of misses.
While manufacturing our custom parts in Canada has worked for us, we’ve advised many of our local peers to offshore some or all of their manufacturing and assembly. At the end of the day, you have to spend the time creating a tailored solution that takes into account what you buy, what volume you buy it in, and your preferred mix of quality, cost, speed, communication, flexibility, stability, and control.
As always, diversify your supply chain. Don’t single source — by supplier, or by region. Always have a backup for high-risk components. And when that fails, find ways to think out of the box and innovate.
Adapting to supply chain complications
The supplier of our switch PCBs recently contacted us due to a lead time increase of 300%. It was a low-risk component that we had single-sourced, and finding an alternative supplier would take equally as long as waiting.
After looking at our options, we decided to buy certain components locally (at a higher cost) and to do the final assembly using our product, the V-One.
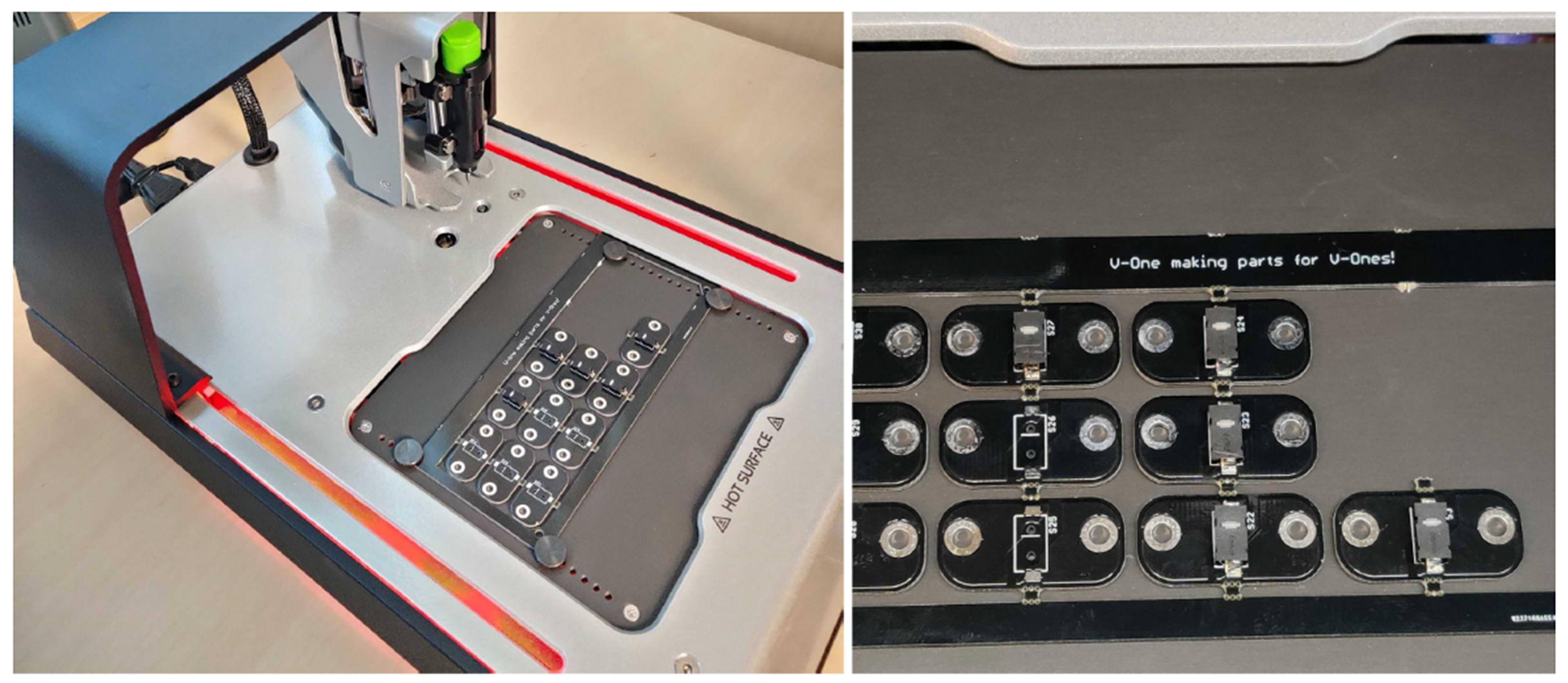
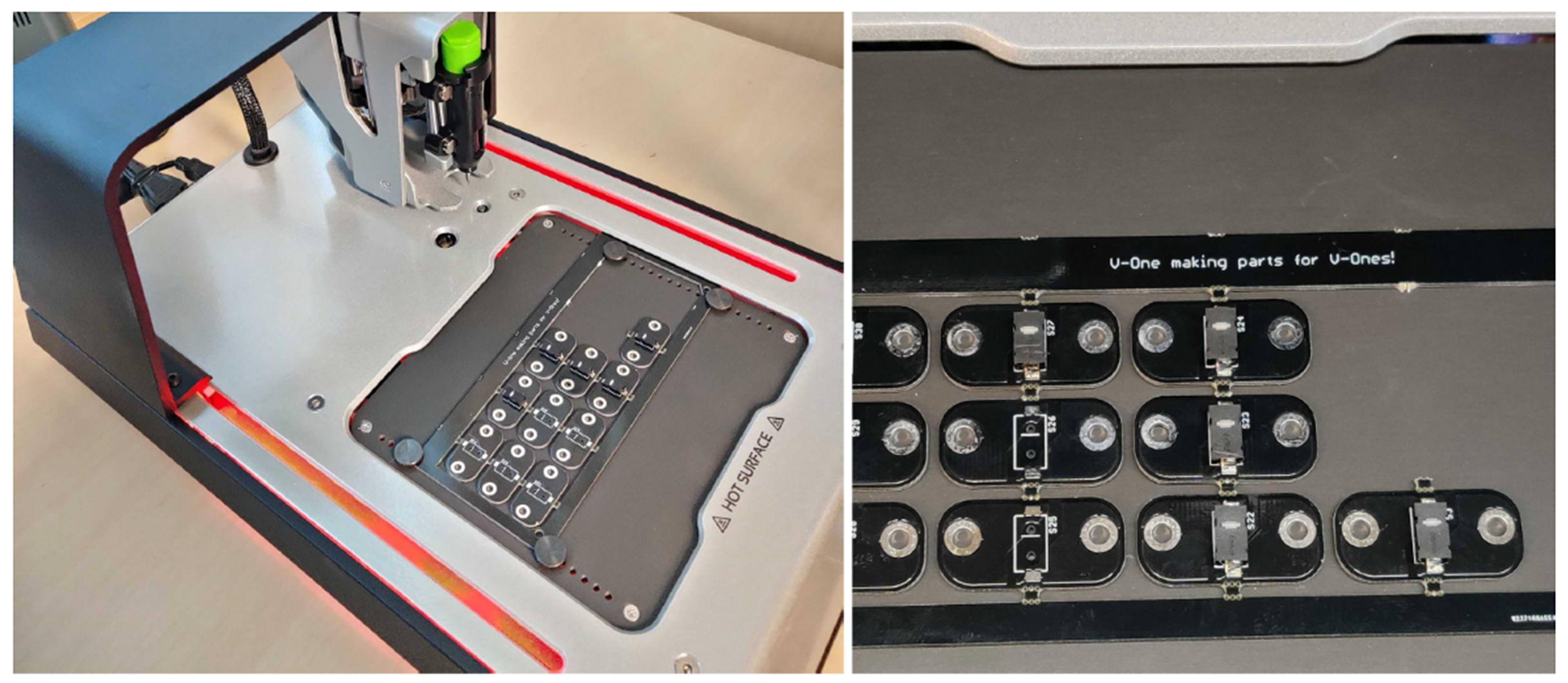
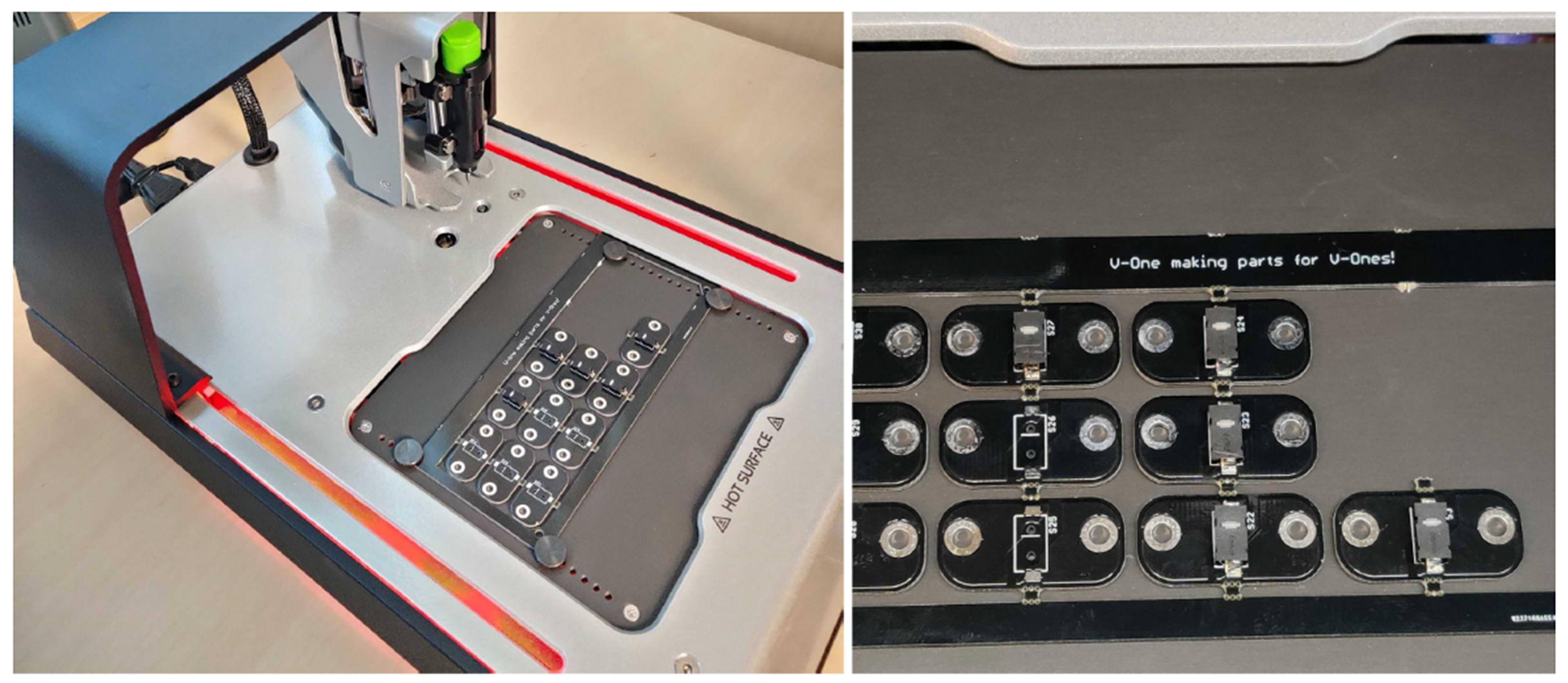
We managed to panelize small boards so we could optimize as much as possible and avoid slowdowns to our production process. It worked beautifully and the results were indistinguishable from the switchboards we received from our supplier.
While this solution doesn’t work for everyone, we found a way to innovate through these hard times. To use a low-volume production tool for medium volume assembly.
As the world continues to reopen for business, it’s important regardless of how small your company is, to re-evaluate your supply chain. This is not the only crisis we’ll face, and this marks a great opportunity to build upon our weaknesses to be even stronger for tomorrow.
I wish you all the best while doing so and hope you and your loved ones are safe and healthy in the coming months.
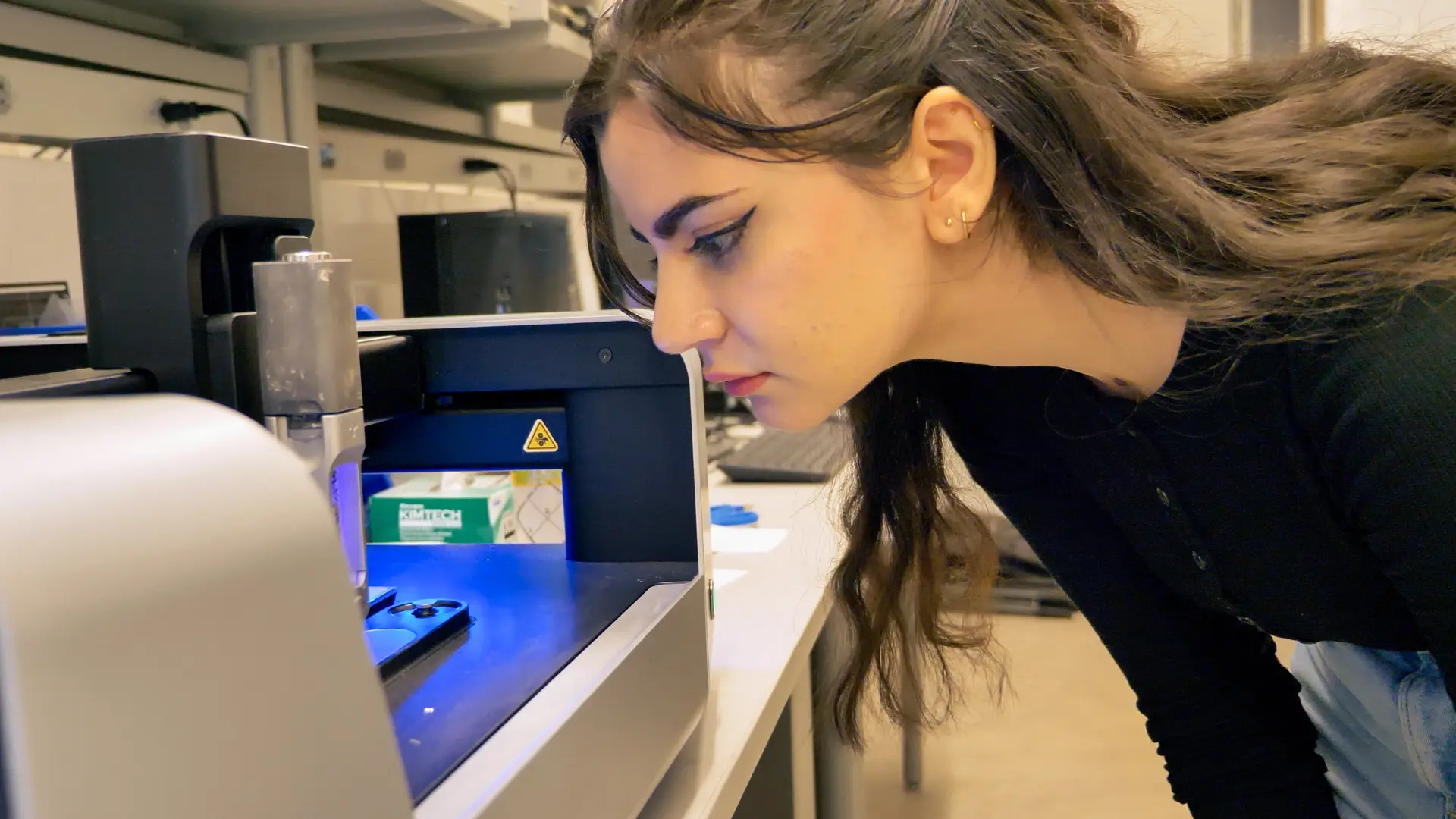
Check out our Customer Stories
Take a closer look at what our customers are doing in the industry.
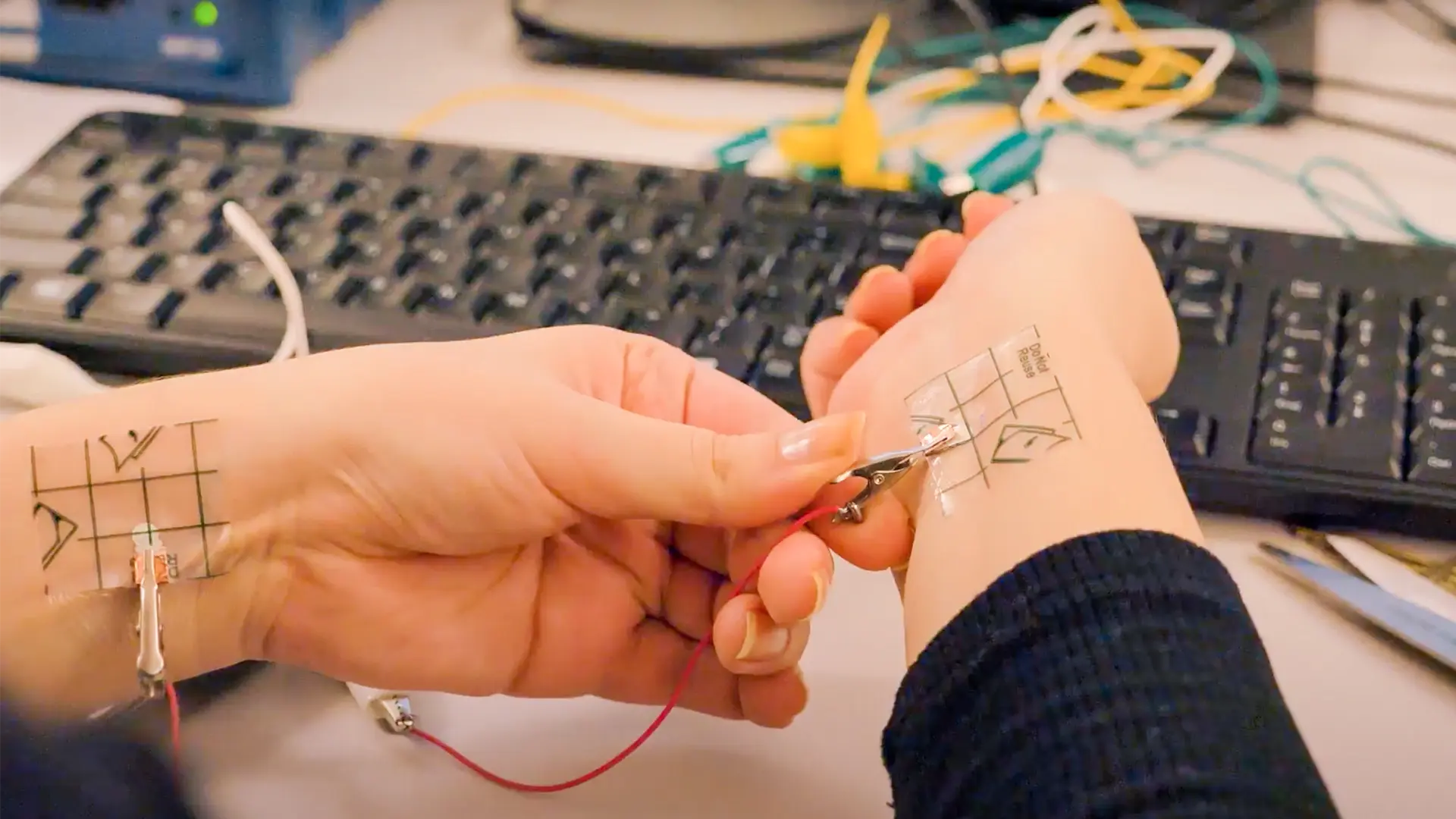