What Is Dot Dispensing?
Researchers and product developers continually push the limits of precision and resolution in material dispensing. Dot dispensing in electronics and other advanced fields such as additive manufacturing, chemical engineering, and biomedicine provides the fine control needed for cutting-edge applications, enabling features such as fine solder paste application, DNA microarrays (a kind of biochip), or adhesive micro dots.
How dot dispensing works
In dot dispensing (a form of drop-on-demand printing), a small volume of functional material is ejected from a nozzle to form a droplet (”dot”) that lands on a substrate at a specified location. Each dot is typically on the order of microliters, nanoliters, or even picoliters in volume.
The process is digitally controlled: each droplet is generated only when and where needed, allowing precise patterning and minimizing waste. By adjusting process parameters (such as pressure pulses or actuator voltage), the system controls the volume of each drop and thus the dot size on the substrate.
Applications of dot dispensing
The applications of dot dispensing include microelectronics packaging (e.g., solder paste, conductive adhesives), flexible printed electronics, microfluidics fabrication, biomaterial and cell-based bioprinting, LED phosphor dispensing, underfill encapsulation, and the construction of microstructured sensors and actuators for electronic skin and wearable technology. They provide high accuracy, repeatability, and scalability critical for complex device fabrication and advanced material development [1].
Types of dot dispensing machines
There are several engineering approaches to generate and dispense tiny dots. Based on one classification framework of Lee J M, et al. [2], dot dispensing mechanisms fall into two broad categories:
- Material jetting: A non-contact method that uses actuation mechanisms such as piezoelectric or solenoid jet valves to eject discrete droplets
- Material extrusion: A contact-based method where material is deposited through pressure-driven flow, including pneumatic time-pressure and positive displacement systems
Each category is suited to a different viscosity range and precision level.
Material jetting
Piezoelectric inkjet dot dispensing machines
Piezoelectric inkjet dispensers use a piezoelectric actuator to create a pressure pulse in a small ink chamber, ejecting a droplet through a fine orifice. They produce extremely small droplets (single picoliters), enabling high-resolution patterning and precise application in the form of thin, accurate deposit dots and lines [3][4].
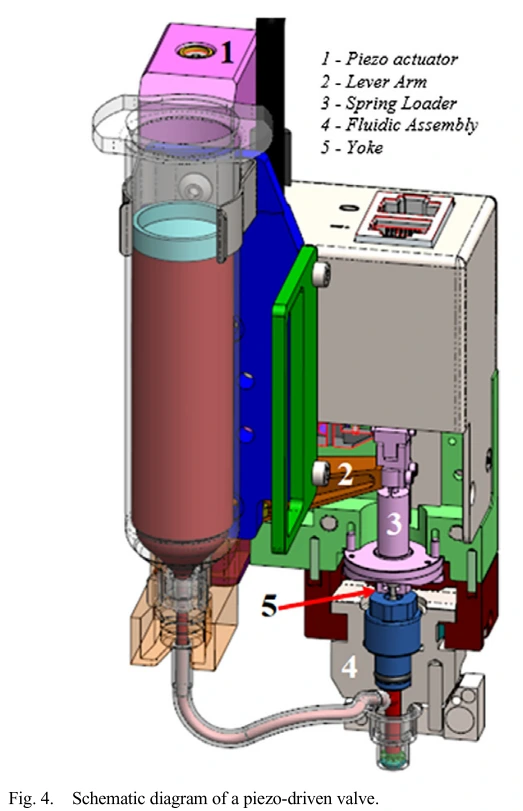
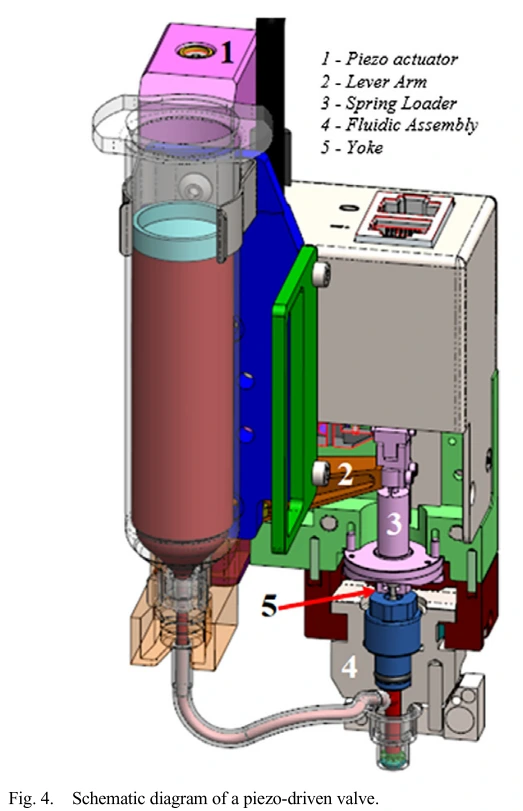
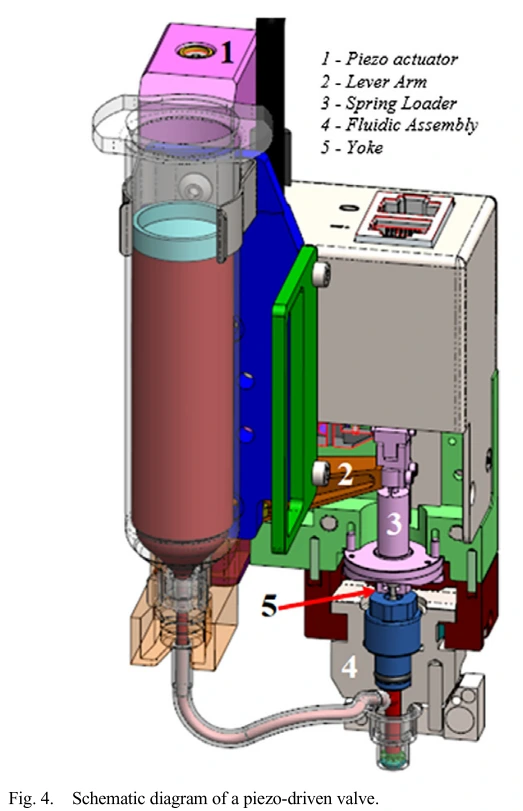
The limitation of piezoelectric inkjet, however, is that they impose strict ink property requirements: typically a viscosity below 40 cP and surface tension in the 20-70 mN/m-1 range for reliable jetting [5]. As such, piezoelectric inkjet dispensers are only suitable for micro volume dispensing of low-viscosity functional inks such as conductive polymers and nanoparticle inks [3].
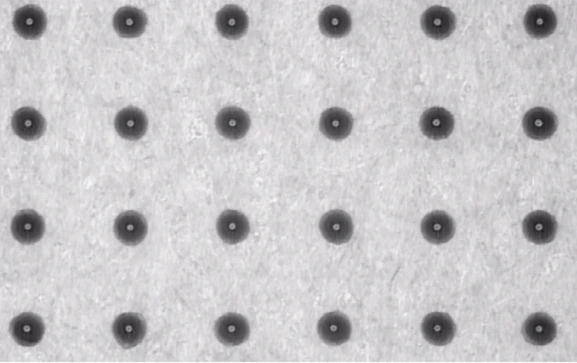
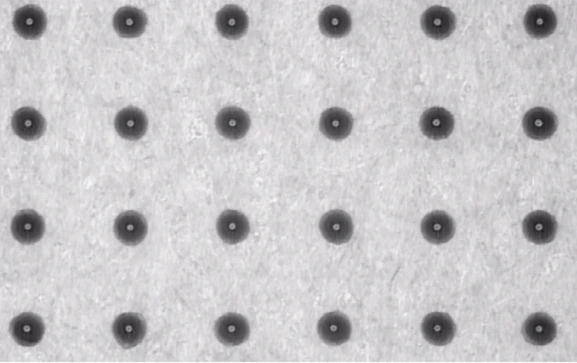
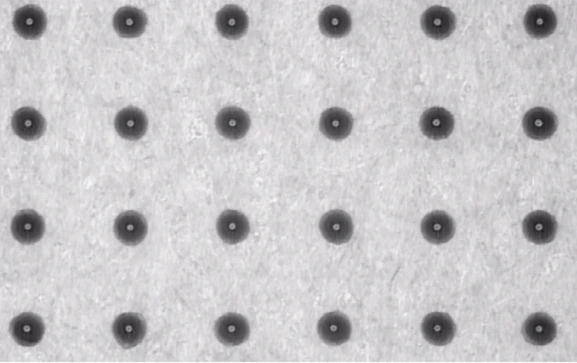
Solenoid jetting dot dispensing machines
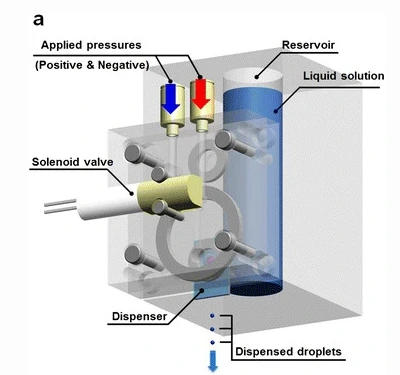
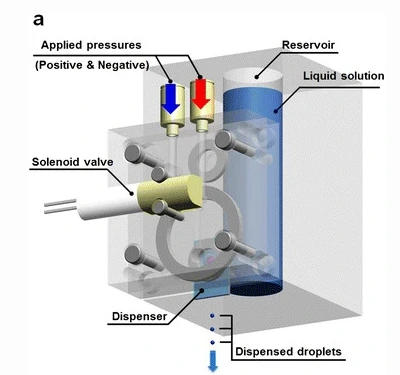
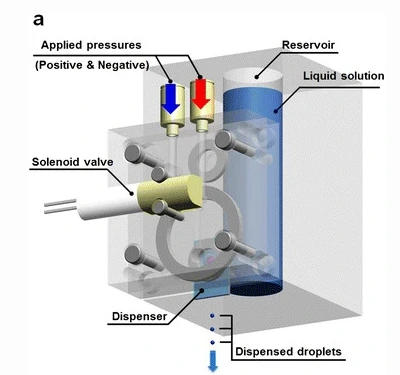
Different from a piezo-actuated valve dispenser, where a piezoelectric stack or bending element drives the needle open and closed, in a solenoid jet valve, a coil generates a magnetic force to lift the valve needle off its seat momentarily, allowing fluid to jet out until the spring or magnetic force closes it again.
Similar to piezoelectric jetting systems, solenoid jetting dispensers excel at very high-speed dotting (up to kHz firing rates) and tiny dot sizes (tens of microns), but can handle viscosities up to about 40 cP. Although researchers have been experimenting with pushing jetting into the higher viscosity range, challenges of pattern fidelity remain to be solved.
In addition, a material jetting system is more complex than a simple time-pressure syringe. It requires a precision-machined valve assembly and a dedicated driver (for the solenoid or piezo). These systems are often more expensive per dispense head than a basic pneumatic time-pressure dispenser, limiting their scalability.
Material extrusion
Pneumatic time-pressure dot dispensing machines
A time-pressure pneumatic dispenser uses a controlled pressure (air or inert gas) applied to a fluid reservoir to push material through a nozzle. By adjusting pressure and valve open time, discrete droplets can be dispensed [6].
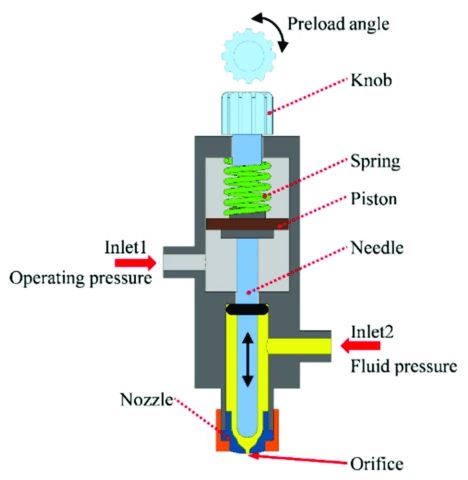
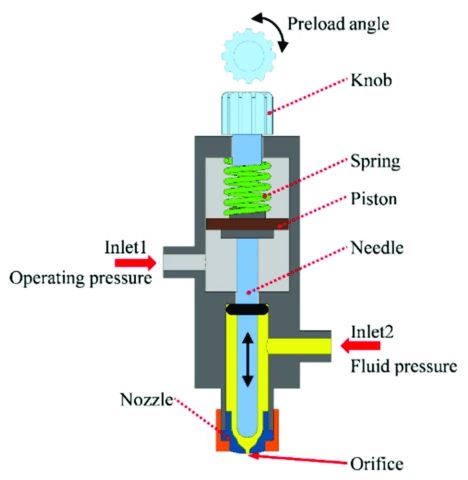
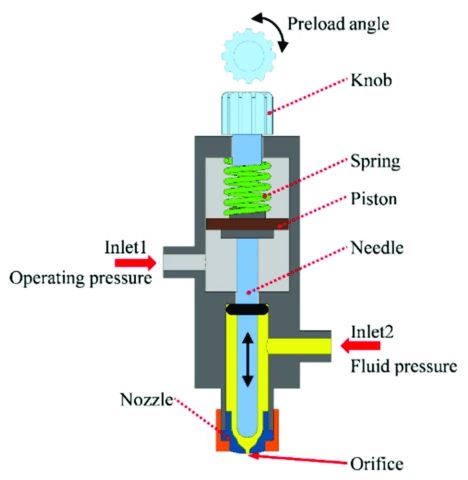
Compared to piezo or microvalve systems, pneumatic dispensers tolerate higher viscosity fluids than inkjet heads (typically 100-100,000 cP), making them versatile in their applications. They are suitable for thick adhesives, silicone sealants, solder pastes, or polymer gels that piezo inkjets cannot eject [7].
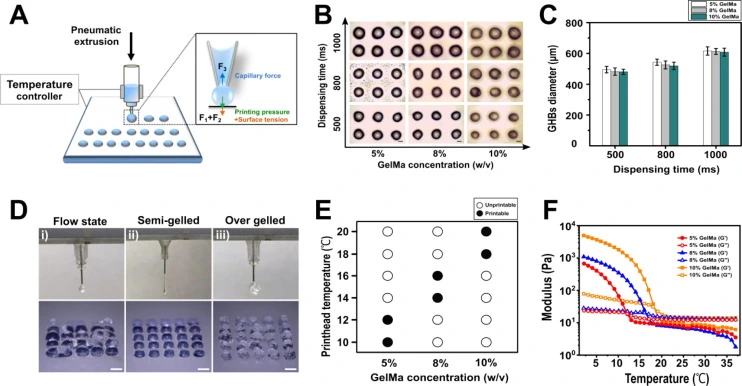
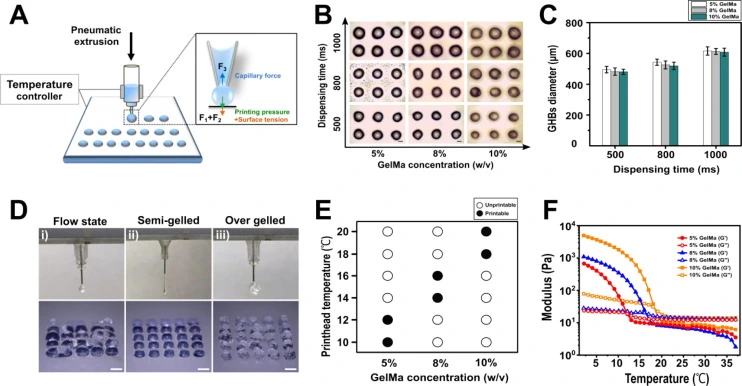
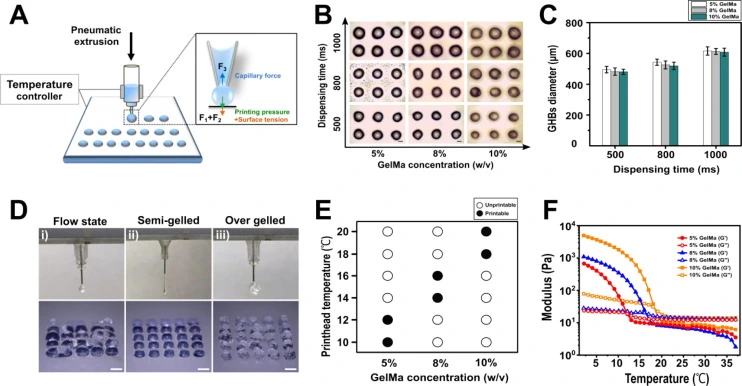
However, the precision and minimum dot size achievable by pneumatic dispensers are more limited. The dispensed volume depends on several factors (pressure level, time, fluid viscosity, nozzle diameter, and even air compressibility) [9], which makes ultra-fine control challenging. Without additional feedback or mechanical pinch-off, achieving very small, consistent dot volumes (in the low-nanoliter range) is difficult due to variability in how the fluid stream breaks off [1].
Positive displacement dot dispensing machines
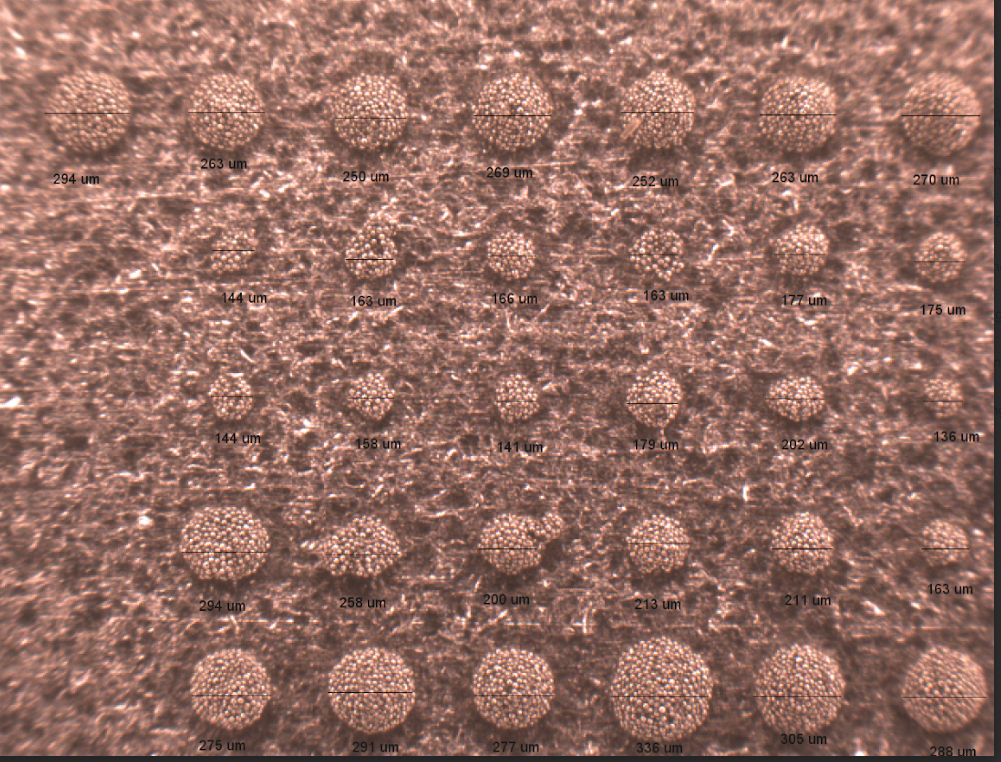
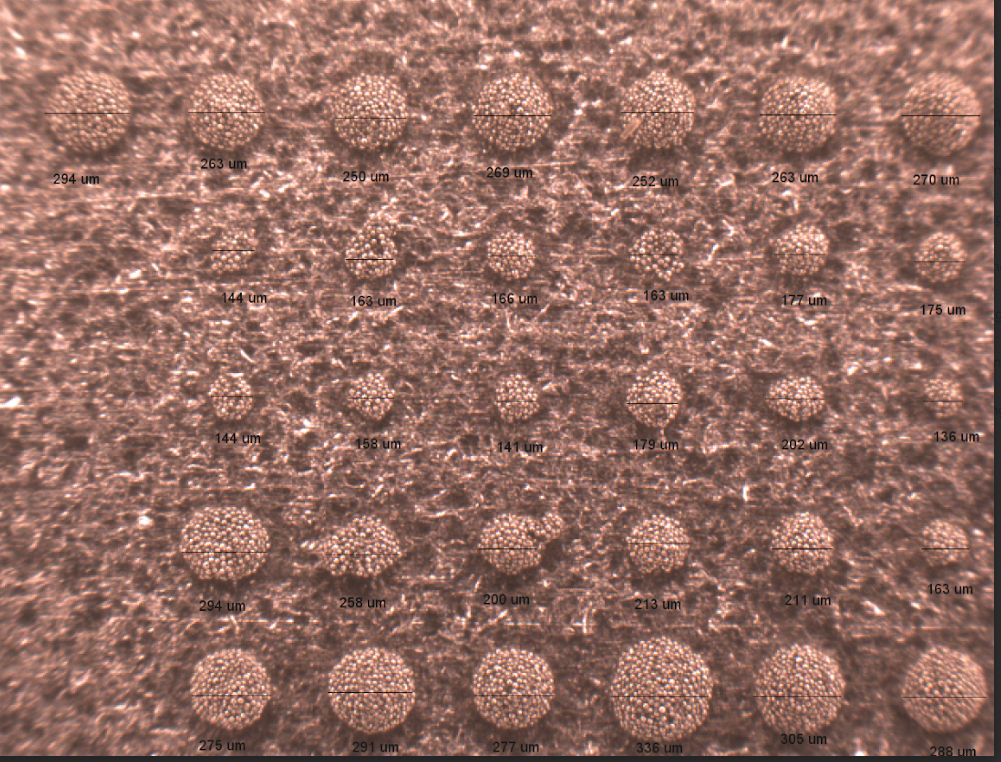
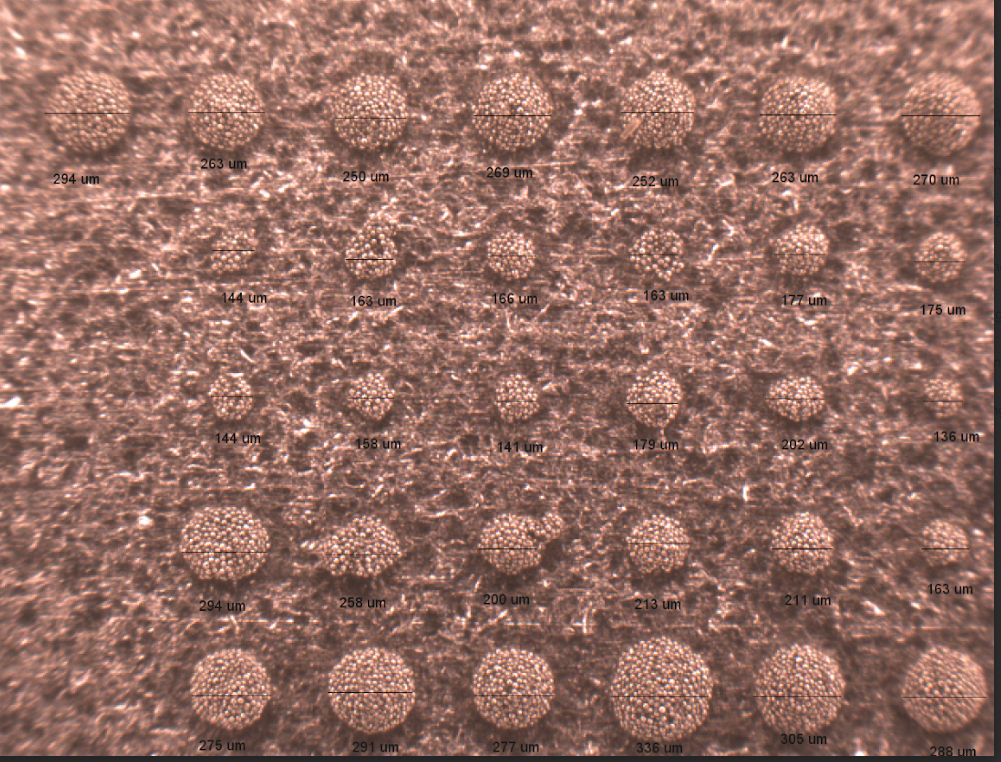
Positive displacement dot dispensing machines use mechanical actuators (e.g., pistons, auger/screws) to directly displace fluid, eliminating air compressibility errors inherent in pneumatic systems. This enables superior volumetric accuracy (< about 1.5% coefficient of variation for 100 nL volumes) and precise control over high-viscosity fluids (up to 1,000,000 cP) [10].
Extrusion-based direct ink writing equipment, such as NOVA (pressure-feedback positive displacement dispensing), falls into this category, capable of accommodating highly viscous, paste-like inks that are orders of magnitude thicker than inks for inkjet dispensers. For example, silver-filled conductive adhesives with nano- or micro-particles, or solder paste with metal alloy powder, can be dispensed by DIW systems when they would clog a fine inkjet nozzle. The ability to deposit such high-solids, thixotropic fluids is a key advantage of extrusion-based dot dispensing [9].
Conclusion
Dot dispensing technology continues to evolve, expanding its scope into new materials and applications. Improvements in actuator design, fluidics, and control software are pushing the boundaries of what can be dispensed in tiny dot form. By choosing the appropriate dispensing mechanism for a given material and feature size, scientists and engineers can reliably deposit microscopic amounts of material exactly where needed, enabling the fabrication of next-generation devices and materials, one tiny drop at a time.
Want to learn more about materials dispensing? Explore these resources:
- Blog: What are Precision Fluid Dispensing Systems?
- Blog: What is Viscosity?
- Blog: High-Resolution Electronics Prototyping: Pushing the Limits with Closed-Loop Dispensing Systems
- Video: Dot, Dot, Dot...Optimized Dispensing for Silver-Filled Conductive Epoxy Adhesives
Ready to discuss your dot dispensing needs? Book a meeting to speak with one of our technical representatives.
References
[1] Lee, S., Choi, I. H., Kim, Y. K., & Kim, J. (2014). Velocity control of nanoliter droplets using a pneumatic dispensing system. Micro and Nano Systems Letters, 2(1). https://doi.org/10.1186/s40486-014-0005-8.
[2] Lee, J. M., Sing, S. L., Zhou, M., & Yeong, W. Y. (2018). 3D bioprinting processes: A perspective on classification and terminology. International Journal of Bioprinting, 4(2). https://doi.org/10.18063/ijb.v4i2.151.
[3] Bernasconi, R., Brovelli, S., Viviani, P., Soldo, M., Giusti, D., & Magagnin, L. (2021). Piezoelectric Drop‐On‐Demand Inkjet Printing of High‐Viscosity Inks. Advanced Engineering Materials, 24(1), 2100733. https://doi.org/10.1002/adem.202100733.
[4] Ng, W. L., Lee, J. M., Yeong, W. Y., & Win Naing, M. (2017). Microvalve-based bioprinting – process, bio-inks and applications. Biomaterials Science, 5(4), 632–647. https://doi.org/10.1039/c6bm00861e.
[5] Tsai, H.-L., Hwang, W.-S., Wang, J.-K., Peng, W.-C., & Chen , S.-H. (2015). Fabrication of Microdots Using Piezoelectric Dispensing Technique for Viscous Fluids. Materials, 8(10), 7006–7016. https://doi.org/10.3390/ma8105355.
[6] Durham, M., Wade, G., Judd, B., & Boggiatto, J. (n.d.). Process Optimization for Fine Feature Solder Paste Dispensing. Retrieved May 9, 2025, from https://www.ipc.org/system/files/technical_resource/E40%26S16_01%20-%20Maria%20Durham.pdf.
[7] Xiao, X., Li, G., Liu, T., & Gu, M. (2022). Experimental Study of the Jetting Behavior of High-Viscosity Nanosilver Inks in Inkjet-Based 3D Printing. Nanomaterials, 12(17), 3076. https://doi.org/10.3390/nano12173076.
[8] Wei, X., Huang, B., Chen, K., Fan, Z., Wang, L., & Xu, M. (2022). Dot extrusion bioprinting of spatially controlled heterogenous tumor models. Materials & Design, 223, 111152. https://doi.org/10.1016/j.matdes.2022.111152.
[9] Polychronopoulos, N. D., & Angeliki Brouzgou. (2024). Direct Ink Writing for Electrochemical Device Fabrication: A Review of 3D-Printed Electrodes and Ink Rheology. Catalysts, 14(2), 110–110. https://doi.org/10.3390/catal14020110.
[10] Ando, T., Hirano, M., Ishige, Y., & Adachi, S. (2016). Precise Dispensing Technology Using Electroformed Tubes for Micro-Volume Blood Diagnosis. IEEE journal of translational engineering in health and medicine, 6, 2800506. https://doi.org/10.1109/JTEHM.2018.2852664.
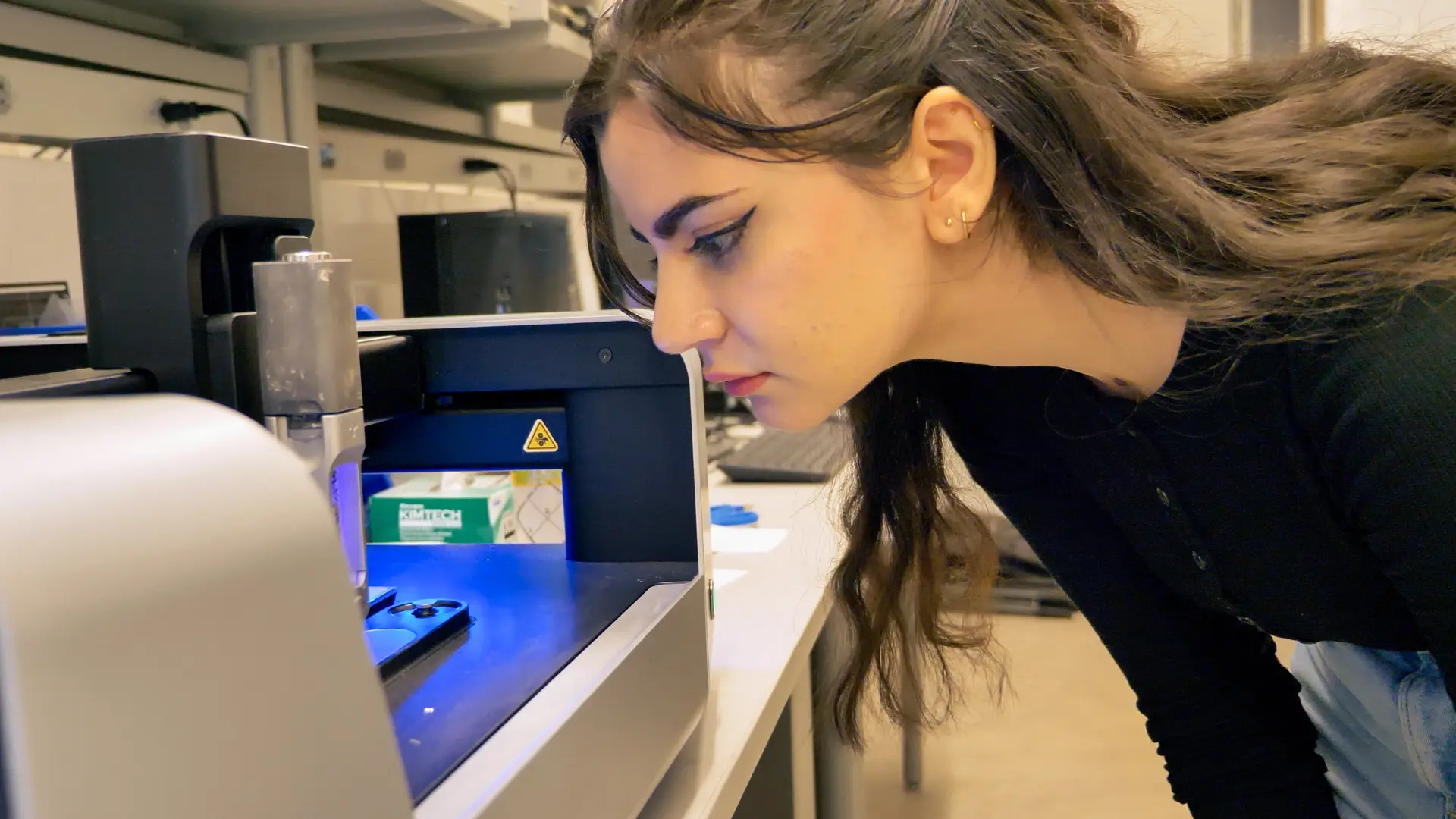
Check out our Customer Stories
Take a closer look at what our customers are doing in the industry.
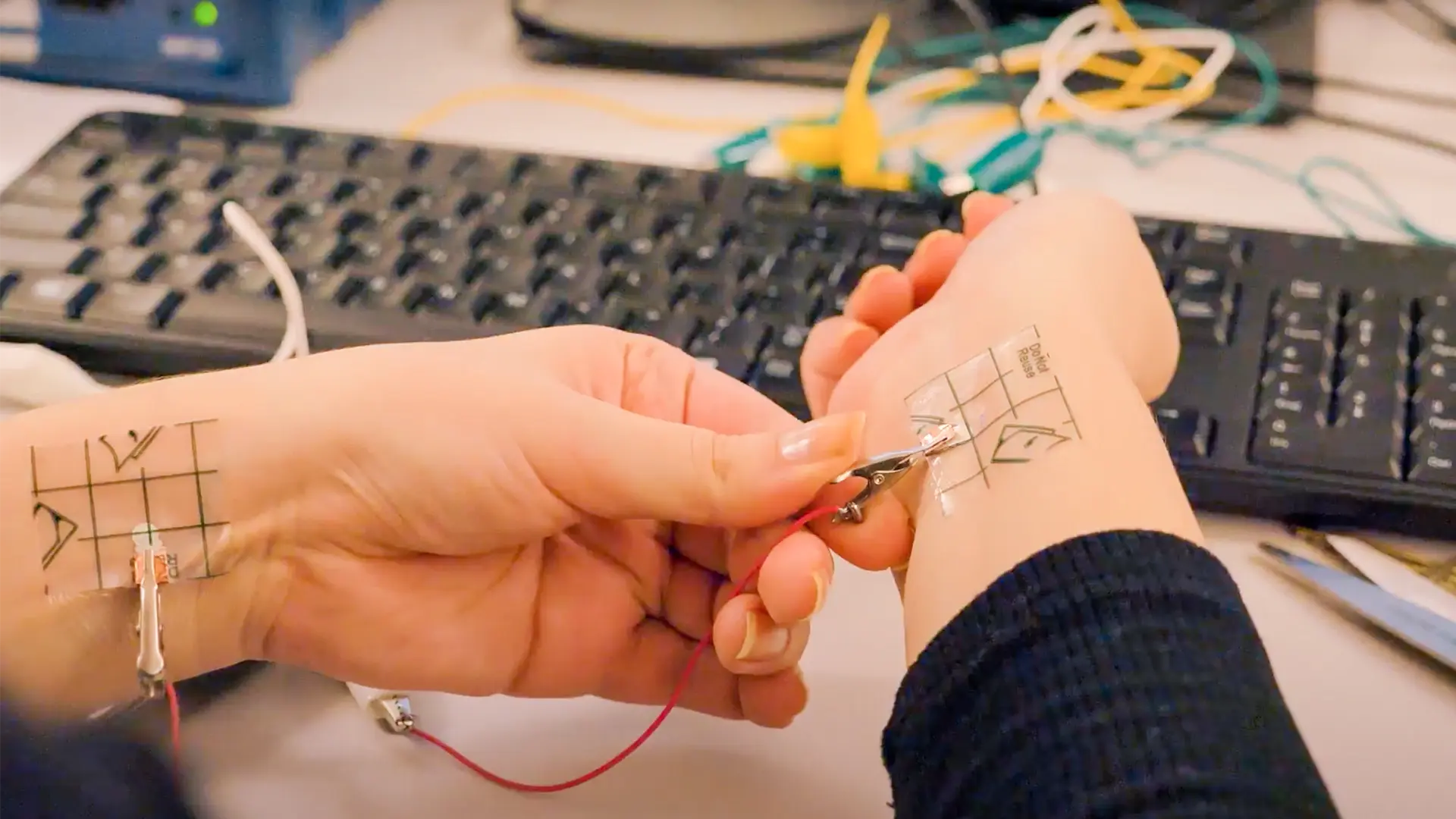